Ink Zone Control: an Upgrade that Quickly Pays Off
At every printing press, precise control of the printing image is essential for immaculate print products, resulting in turn in satisfied customers. With the retrofitted ink zone control system, corrections are transferred to the substrate in a split second. That makes production considerably more cost-effective.
The electronic ink zone control system, which can be installed in all Muller Martini printing presses and the Drent VSOP/Vision, was developed in-house by Muller Martini. It sets high standards in terms of precision, speed, reliability, and ease of use. Equipping of the existing sliders or knife-type inking systems with fully integrated automation and simple touch-screen operation ensures optimal control of the ink density. The upgrade enables discontinued ink zone systems to be brought in line with the technical state of the art. Retrofitting of inking systems supplied ex works with manual sliders is also possible.
The ink zone control kit consists of identical components to those used for new machine production, and a specific Muller Martini development team ensures that the technology used remains cutting edge. An example of that is the ink zone control box that was developed specifically for the retrofit kit. It is used per printing unit to control the 16, 21, 23 or 28 ink zones at each printing unit and to ensure communication with visualization.
All key components are produced in the Muller Martini supplier plants, enabling discontinued systems to be professionally and promptly brought up to date using replacement components. A CIP3/CIP4 interface and a network connection are also optionally available, allowing ink zones to be pre-set using pre-press data. That shortens setup times considerably and prevents production waste.
Florian Bächler, Managing Director at Bächler-Sidler AG, confirms that the retrofitting of an ink zone control system is attractive in terms of both cost-effectiveness and quality. Setup times and production waste have both been halved at the 20-year-old A68 web printing press of the printing plant in Lucerne (Switzerland). To satisfy current market requirements, especially in the mailshot segment, the replacement of its ink zone control system, which was performed in four days, was a matter of urgency. “Since our product range has changed, we perform twice as many changeovers today as when we commissioned the A68, so we urgently needed to reduce the setup times,” says Florian Bächler.
The head of the family business also evaluated third-party suppliers during the quotation phase for the update, but opted for the original for three key reasons. “First, Muller Martini has made a clear commitment to its web offset printing customers by developing the new ink zone control system. Second, I’m impressed by the MMServices.Print offering. And, third, Muller Martini presented us with an impressive overall upgrade concept, which means our A68 will stay up to date for the next five to ten years.”
The ink zone control system is just one of numerous service modules that Muller Martini offers the owners of over 2,000 Muller Martini printing presses worldwide under its MMServices.Print label. Whether you need spare parts or help with repairs, or have questions about the use of your equipment, Muller Martini’s printing press experts are here to assist you by telephone, remotely, or on site. With advanced repair and maintenance concepts, updates, upgrades, reconditioning and training for machine operators, Muller Martini’s MMServices.Print provides long-lasting investment protection.
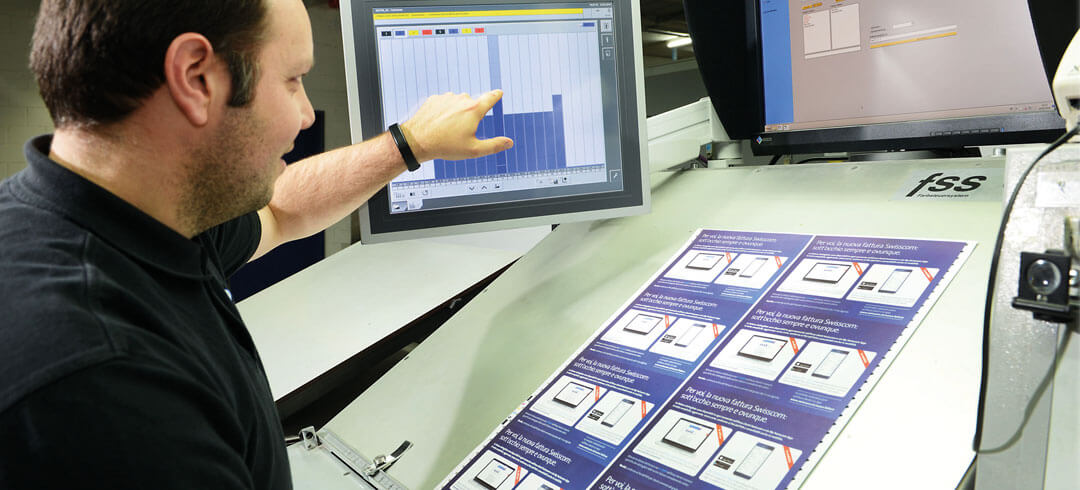
Muller Martini’s electronic ink zone control system was developed by Muller Martini, and sets high standards in terms of precision, speed, reliability, and ease of use.